You’re about to explore the intricate process of Harley-Davidson bike production, which combines traditional craftsmanship and cutting-edge technology. You’ll see how the factory layout optimizes production efficiency and minimizes waste. As you look closer, you’ll discover the highly coordinated bike assembly process and innovative technology used to produce these iconic bikes. You’re just getting started on a journey that reveals the precision and craftsmanship behind every Harley-Davidson bike.
Key Takeaways
- Harley-Davidson’s production started in 1903.
- Factory tours show the bike production process.
- Workstations optimize production efficiency.
- Engine production is a critical component.
- Quality control ensures high standards.
History of Harley-Davidson Manufacturing
As you explore into the history of Harley-Davidson manufacturing, you’ll find that the company’s production roots date back to 1903, when William S. Harley and Arthur Davidson started building bikes.
During a factory tour, you’ll see how Harley-Davidson bike production has evolved over the years. You’ll learn about the company’s early days, when it produced just a few bikes per year, to its current status as a global manufacturer.
Witness the evolution of Harley-Davidson bike production on a factory tour.
The factory tour will give you a behind-the-scenes look at the bike production process, from design to assembly. You’ll see the latest technology and manufacturing techniques used to produce Harley-Davidson bikes.
The tour will provide a detailed understanding of the company’s history and production processes, giving you a new appreciation for the iconic Harley-Davidson brand. You’ll gain insight into the company’s commitment to quality and innovation.
Factory Layout and Design
You’ll examine the factory layout, which is vital for efficient bike assembly, as it determines the placement of workstations, equipment, and personnel.
As you assess the bike assembly process, you’ll consider how it’s organized into sequential stages, each with its own set of tasks and quality control checks.
You’ll analyze the production line, where Harley-Davidson bikes take shape, and evaluate how it’s designed to optimize workflow, reduce waste, and increase productivity.
Factory Layout
The factory layout at Harley-Davidson’s manufacturing facilities is designed to optimize production efficiency and minimize waste.
You’ll notice that workstations are strategically placed to reduce material handling and transportation costs.
The facilities are divided into separate areas for receiving, inspection, and storage of raw materials.
You see a structured flow of components and subassemblies, ensuring that all necessary parts are readily available.
This layout enables Harley-Davidson to streamline its operations, reducing production time and increasing overall productivity.
It allows you to visualize the entire production process, from raw materials to finished components.
Bike Assembly
Harley-Davidson’s bike assembly process is a highly coordinated and efficient operation, with each station on the production line playing a critical role in bringing together the various components and subassemblies.
You’ll notice that the factory layout is designed to optimize workflow, with workstations arranged to minimize movement and maximize productivity.
As you walk through the assembly area, you’ll see that each station is equipped with specialized tools and equipment, allowing technicians to focus on specific tasks, such as engine installation or wiring harness assembly.
This setup enables you to efficiently assemble bikes with precision and accuracy.
Production Line
Factory layout and design play a crucial role in optimizing production line efficiency, and manufacturers like Harley-Davidson carefully plan their facilities to streamline workflows.
You’ll notice that production areas are divided into separate zones, each with its own specific function.
As you walk through the facility, you’ll see that the layout is designed to minimize material handling and reduce travel distances.
This enables Harley-Davidson to produce bikes more efficiently, with reduced lead times and increased productivity.
You can see how the production line is organized to maximize efficiency, allowing the company to meet high demand for its iconic bikes.
Bike Assembly Process
You’re about to witness the transformation of individual components into a fully assembled Harley-Davidson bike, starting with the bike frame, which is carefully constructed to meet precise specifications.
As you observe the assembly line, you’ll notice that it’s divided into distinct stations, each responsible for adding specific parts to the frame, such as the engine, transmission, and suspension.
You’ll see how the bike takes shape as it moves along the assembly line, with skilled technicians and automated systems working together to guarantee a high level of quality and consistency.
Bike Frame
The bike frame is a critical component in the bike assembly process, and it’s where you’ll start building the foundation of your Harley-Davidson motorcycle.
You’ll begin by inspecting the frame for any defects or irregularities. The frame’s material, usually steel or aluminum, is carefully selected for its strength and durability.
You’ll then proceed to attach the engine mounts, swingarm, and other key components to the frame. This process requires precision and attention to detail to certify a stable and secure ride.
You’ll be working with precise measurements and specifications to guarantee a perfect fit.
Assembly Line
How precisely do the various components come together to form a Harley-Davidson motorcycle?
You’ll see the frame, engine, and transmission come together on the assembly line.
As you progress through the line, you’ll add the electrical and braking systems.
You’ll then install the wheels, suspension, and steering components.
Finally, you’ll add the fuel tank, seat, and fairings to complete the bike.
You’ll conduct thorough inspections and tests to certify the motorcycle meets Harley-Davidson’s quality standards.
The assembly process requires precision and attention to detail to produce a high-quality motorcycle.
You’ll verify every component is properly installed.
Engine Production and Development
Engine production is a critical component of Harley-Davidson’s bike manufacturing process, with designers and engineers continually developing and refining powertrain systems to meet performance, efficiency, and emissions standards.
You’ll notice that they focus on optimizing engine design, materials, and manufacturing techniques to improve power output, reduce weight, and increase fuel efficiency.
Optimizing engine design for improved power, reduced weight, and increased fuel efficiency.
As you explore the engine production process, you’ll see that it involves precise machining, assembly, and testing of components, including cylinders, pistons, and crankshafts.
You’ll also find that Harley-Davidson uses advanced technologies, such as computer-aided design and simulation, to validate engine performance and reliability.
By continually improving engine production and development, Harley-Davidson can deliver high-quality, high-performance bikes that meet the demands of riders like you.
This attention to detail certifies that every engine meets the company’s high standards.
Customization and Painting Procedures
You’ll take your Harley-Davidson bike to a whole new level with customization options that let you personalize its look and feel.
You can choose from various paint schemes, decals, and accessories to create a unique bike. The painting process involves a multi-step procedure, including surface preparation, primer application, and paint coating.
You’ll select from a range of colors and finishes, such as metallic, pearl, or matte. The paint is then applied using a robotic system, ensuring a precise and consistent finish.
Additionally, you can add custom decals, stripes, or graphics to enhance the bike’s appearance. The customization options allow you to tailor your Harley-Davidson bike to your preferences, making it a one-of-a-kind vehicle.
Quality Control and Testing Measures
The Harley-Davidson bike production process incorporates rigorous quality control and testing measures to guarantee each vehicle meets the company’s high standards.
You’ll find that every bike undergoes a series of inspections, starting with the frame and engine. As you move through the production line, you’ll notice that each component is carefully examined for defects or irregularities.
You’re checking for proper fitment, function, and performance. The testing measures include dyno tests, which evaluate the engine’s power output and efficiency.
Checking for proper fitment, function, and performance ensures optimal bike operation.
You’re also conducting road tests to assess handling, braking, and overall ride quality. By doing so, you certify that every Harley-Davidson bike that leaves the factory meets the company’s strict quality and performance requirements.
You’re verifying that every bike is reliable, durable, and meets the expectations of Harley-Davidson’s loyal customers.
Innovative Technology and Robotics
You’re about to explore how Harley-Davidson incorporates innovative technology and robotics in its bike production, specifically through the use of robot arms that enhance assembly efficiency.
You’ll examine the role of laser cutting, which enables precise metal fabrication, and its impact on the manufacturing process.
Robot Arms
As Harley-Davidson integrates innovative technology and robotics into its bike production, robot arms play a crucial role in streamlining manufacturing processes.
You’ll notice that robot arms are designed to perform precise tasks, such as welding and assembly. They’re equipped with advanced sensors and control systems, allowing for accurate and efficient operation.
You can see robot arms working in tandem with human workers, increasing productivity and reducing production time.
This integration of robot arms enables Harley-Davidson to produce high-quality bikes with consistent results, meeting the company’s strict standards. You’re witnessing a significant improvement in manufacturing efficiency.
Laser Cutting
Robot arms’ precision tasks, like welding and assembly, set the stage for another innovative technology: laser cutting.
You’ll see lasers cutting complex shapes with high accuracy, utilizing computer-aided design (CAD) software. This process enables you to cut various materials, such as steel and aluminum, with minimal waste.
Laser cutting’s precision and speed allow for increased efficiency in Harley-Davidson’s production line. You can observe the laser’s beam, focused to a precise point, cutting through materials with ease, demonstrating the technology’s capabilities in producing intricate bike components.
This technology enhances the manufacturing process, ensuring consistent quality.
Metal Stamping
The metal stamping process at Harley-Davidson leverages innovative technology and robotics to produce complex components with high precision.
You’ll see robotic arms handling metal sheets, feeding them into stamping machines. These machines use advanced tooling to shape and form the metal into required components.
You’re able to monitor the process closely, ensuring accuracy and quality. The metal stamping process allows for high-volume production, making it an essential part of Harley-Davidson’s manufacturing process.
It enables the production of components like engine mounts and brake components with tight tolerances and precise dimensions. You can observe the entire process, from start to finish.
Employee Training and Expertise
Manufacturing high-quality Harley-Davidson bikes requires skilled workers who undergo rigorous employee training and expertise development. You’ll find that employees participate in ongoing training programs to enhance their skills.
Training Type | Duration | Frequency |
---|---|---|
Welding | 6 months | Quarterly |
Engine Repair | 3 months | Bi-annually |
Quality Control | 2 months | Annually |
Assembly | 4 months | Semi-annually |
Safety Procedures | 1 month | Monthly |
As you explore the facility, you’ll notice that workers are constantly updating their expertise to meet the company’s high standards. This guarantees they can produce exceptional bikes with precision and accuracy.
Manufacturing Techniques and Materials
You’ll find that Harley-Davidson’s production process relies heavily on precision techniques, such as computer-aided design (CAD) and computer numerical control (CNC) machining, to guarantee accuracy and consistency in every bike.
As you explore the manufacturing process, you’ll notice the use of high-quality materials.
Some key components include:
- Steel and aluminum alloys for frame and engine construction
- High-strength plastics for fairings and bodywork
- Advanced composites for specialized parts
- Forged and cast metals for engine and transmission components
- High-performance coatings for corrosion resistance and durability.
You’ll see that these materials are carefully selected to certify the bikes meet Harley-Davidson’s standards for performance, reliability, and style.
Final Inspection and Preparation for Delivery
As Harley-Davidson bikes near completion, they undergo a rigorous final inspection, where skilled technicians scrutinize every detail to certify each bike meets the company’s stringent standards.
You’ll notice technicians checking the engine, transmission, and brakes to guarantee they’re functioning properly. They’ll also verify that all electrical systems, including lighting and instrumentation, are working correctly.
You’ll be inspecting the bike’s frame, suspension, and wheels to guarantee they’re properly aligned and secured. Additionally, technicians will test the bike’s performance, checking for any issues with acceleration, braking, or handling.
Once the inspection is complete, the bike is prepared for delivery, which includes cleaning, packaging, and loading onto a truck or train for transportation to dealerships. You’ll verify that each bike is carefully secured to prevent damage during transit.
Frequently Asked Questions
Can I Tour the Factory?
You’re wondering if you can tour a factory.
Yes, you can, but it depends on the facility.
You’ll need to check the company’s website for guided tour options. You’ll likely find a schedule and booking information online.
You’ll probably need to register in advance, and you’re expected to follow safety rules during the tour.
Are Bikes Made in Other Countries?
A global wave sweeps you: are bikes made in other countries?
You’re exploring international manufacturing.
Harley-Davidson produces bikes in the US, but you’ll also find facilities in India, Brazil, and Thailand, where they assemble and manufacture bikes, adhering to strict quality standards, and meeting local demand, while still maintaining their iconic American heritage and quality.
How Long Is the Warranty?
You’re wondering how long the warranty is. Typically, it’s 2 years, but you’ll find that some manufacturers offer longer periods.
You’ll need to check the specifics, as it can vary. You’re looking for detailed info, so you’ll want to review the contract, and you’ll see that it covers parts and labor, but you’ll need to follow the maintenance schedule to keep it valid.
Can I Customize My Bike?
You’re a master painter, and your bike’s a canvas.
Can you customize it? Yes, you can tailor your ride with accessories, modifying it to fit your style.
You’re free to upgrade or change parts, making it uniquely yours, with options like custom paint, seats, or handlebars, allowing you to personalize your bike to perfection.
Are Used Bikes Refurbished?
You’re wondering if used bikes are refurbished.
Typically, you’ll find that used bikes undergo inspections, and some are refurbished.
You’ll see that dealerships and owners often repair or replace worn parts, restoring the bike to a safe, operable condition.
You can expect refurbished bikes to have updated components, ensuring they meet safety standards.
Conclusion
You’re the master builder, crafting a mechanical symphony, as Harley-Davidson’s production comes full circle. The factory’s a well-oiled machine, where precision and skill converge, much like a conductor leading an orchestra. With each bike, you’ve orchestrated a masterpiece, fine-tuned for performance, and now it’s ready to hit the road, a badge of honor to innovative manufacturing and technical expertise.
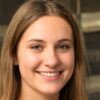
Introducing Michelle, our meticulous planner and talented visual storyteller. She has a knack for discovering those hidden gems, chic boutique spots, and charming little cafes that add a touch of elegance to every journey. With her keen eye for photography and her passion for travel, Michelle will transport you to the most enchanting corners of the world, inspiring you to explore new places, one picture-perfect destination at a time.